LEAN MANGEMENT
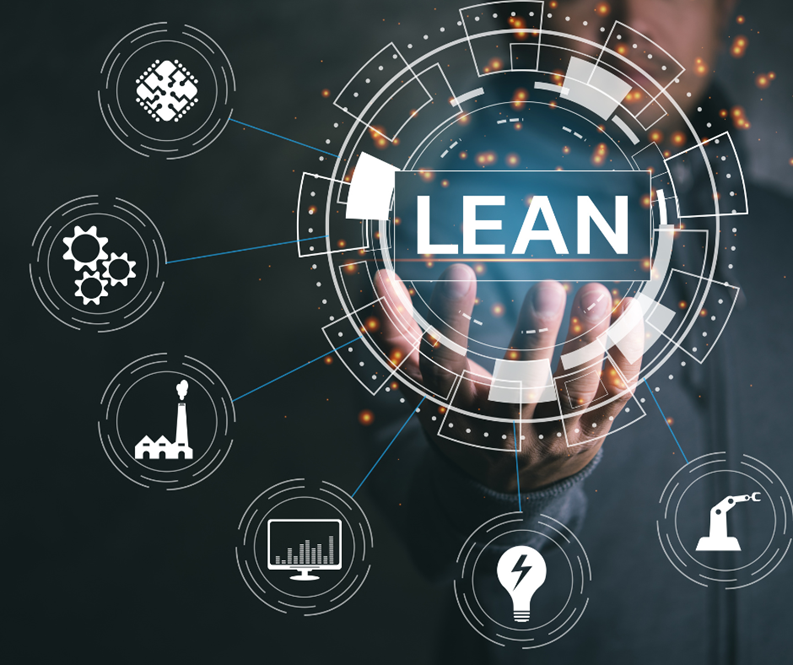
Chapitre 1 : Fondements du Lean Management
1.Définition du Lean Management
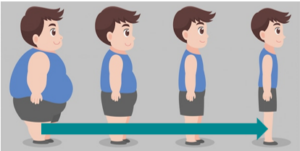
Le Lean Management, souvent appelé simplement « Lean », est une approche de gestion qui se concentre sur l’efficacité opérationnelle en éliminant les gaspillages et en optimisant les processus pour créer une valeur maximale pour le client.
Cette philosophie de gestion trouve ses racines dans le système de production Toyota au Japon, développé dans les années 1950 par Taïchi Ohno et Shigeo Shingo. Comprendre la définition du Lean Management est crucial pour toute organisation qui cherche à améliorer son efficacité opérationnelle. En intégrant les principes fondamentaux du Lean, les entreprises peuvent non seulement améliorer leur rentabilité, mais aussi renforcer leur compétitivité et leur agilité sur le marché.
2.Histoire et origine du Lean
Le Lean Management tire ses racines du système de production révolutionnaire développé par Toyota au Japon dans les années 1950. À l’époque, le secteur automobile japonais cherchait des moyens innovants pour surmonter les défis de la reconstruction d’après-guerre et de la compétition avec les constructeurs automobiles occidentaux.
2.1- Les Pionniers du Lean

Taïchi Ohno
Considéré comme le père du système de production Toyota, Taïchi Ohno a été le principal architecte du Lean.
Il a introduit des concepts tels que la réduction des gaspillages, la production juste-à-temps (Just-In-Time), et le système « Kanban » pour gérer les flux de production de manière efficace.
<
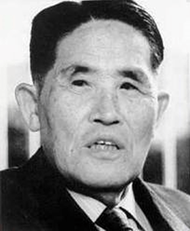
Shigeo Shingo
Collaborateur d’Ohno, Shingo a contribué au développement de concepts tels que le Poka-Yoke (dispositifs anti-erreurs) et le SMED (Single Minute Exchange of Die), visant à réduire les temps de changement d’outils.
2.2- Les Circonstances Historiques
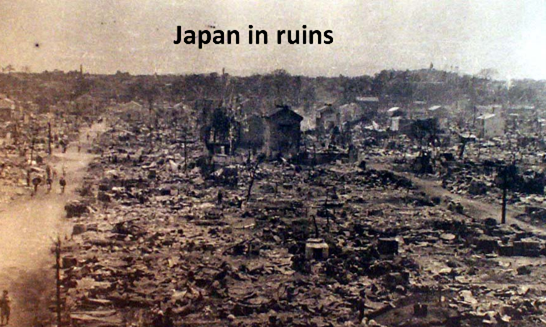
Après la Seconde Guerre mondiale : Le Japon, dévasté par la guerre, a dû reconstruire son économie. Les ressources étaient limitées, et les entreprises japonaises devaient trouver des moyens innovants de produire efficacement avec ce qu’elles avaient à disposition.
Inspirations Occidentales : Les idées de gestion de qualité de Deming et Juran, deux experts occidentaux en gestion de la qualité, ont influencé les praticiens japonais. Les Japonais ont adapté ces concepts pour répondre à leurs propres besoins et contraintes.
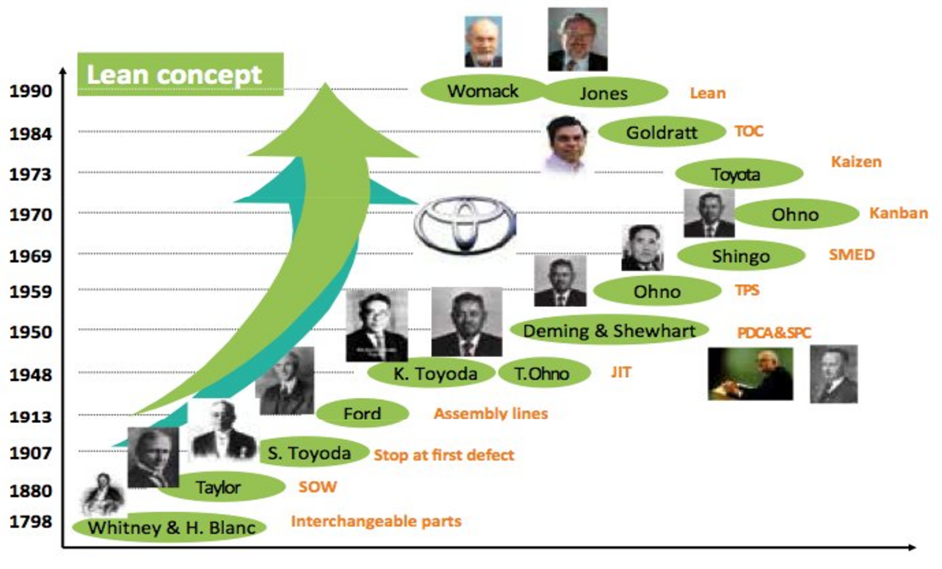
2.3- L’Évolution du Lean dans le Monde
Années 1980 : Expansion Mondiale : À partir des années 1980, les entreprises occidentales ont commencé à adopter les principes du Lean, souvent après avoir observé le succès de Toyota. Le Lean s’est étendu à des secteurs au-delà de la fabrication, y compris les services et les soins de santé.
Popularité Actuelle : Bien qu’il soit apparu au sein de l’industrie automobile, le Lean Management est désormais déployé partout, quels que soient le secteur ou la taille de l’entreprise. Ce concept est d’ailleurs souvent décliné, comme c’est le cas avec le « Lean Purchasing », qui vise l’excellence opérationnelle des services achats.
2.4- Impact sur la Gestion Moderne
Culture d’Amélioration Continue : La philosophie du Lean a introduit une culture d’amélioration continue, incitant les organisations à remettre en question constamment leurs méthodes et à chercher des moyens d’optimiser leurs processus.
Agilité et Adaptabilité : En mettant l’accent sur la flexibilité et l’adaptabilité, le Lean Management permet aux entreprises de réagir plus rapidement aux changements du marché et de rester compétitives dans un environnement en constante évolution.
3.Avantages du Lean Management
Le Lean Management offre une série d’avantages significatifs pour les organisations qui l’adoptent, influençant positivement divers aspects de leur fonctionnement.
3.1- Réduction des coûts : Élimination des gaspillages permettant une utilisation plus efficace des ressources.

L’un des principaux avantages du Lean Management réside dans sa capacité à identifier et à éliminer les gaspillages dans les processus opérationnels.
En éliminant les activités non productives et en optimisant les flux de travail, les entreprises peuvent réduire leurs coûts opérationnels. Cela inclut la réduction des stocks excédentaires, l’optimisation des ressources humaines et matérielles, ainsi que la diminution des temps d’attente. La focalisation sur la valeur ajoutée pour le client permet une allocation plus judicieuse des ressources, contribuant ainsi à l’amélioration de la rentabilité.
3.2- Amélioration de la qualité : Accent sur la détection et la résolution précoce des problèmes.

Le Lean Management met l’accent sur la qualité en favorisant une approche proactive de la détection et de la résolution des problèmes. En éliminant les sources de gaspillages, les processus deviennent plus transparents, facilitant l’identification précoce des défauts ou des erreurs. La mise en œuvre de concepts tels que le Poka-Yoke (dispositifs anti-erreurs) contribue à prévenir les erreurs dès leur apparition.
Une amélioration continue du processus permet non seulement de garantir la qualité des produits ou services, mais aussi d’anticiper et de résoudre les problèmes potentiels avant qu’ils n’affectent significativement la satisfaction du client.
3.3- Flexibilité accrue : Capacité à s’adapter rapidement aux changements de demande.
La flexibilité est un autre avantage clé du Lean Management. En adoptant des principes tels que la production juste-à-temps et la réduction des stocks, les entreprises deviennent plus réactives aux fluctuations de la demande.

Elles peuvent ajuster rapidement leur production en fonction des besoins réels du marché, évitant ainsi les surplus ou les ruptures de stock. Cette flexibilité permet une gestion plus agile des ressources et une meilleure adaptation aux évolutions du marché, renforçant la compétitivité de l’organisation.
3.4- Satisfaction client : Fournir une valeur accrue aux clients grâce à une meilleure qualité et une réactivité accrue.
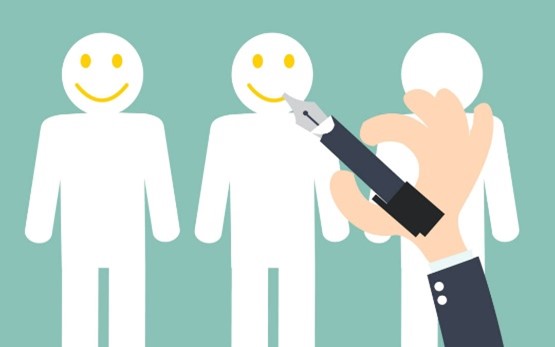
En combinant la réduction des coûts, l’amélioration de la qualité et la flexibilité accrue, le Lean Management contribue directement à la satisfaction client. Les produits ou services sont livrés plus rapidement, avec une qualité supérieure et une réponse plus efficace aux besoins du client.
Les organisations Lean se concentrent sur la création de valeur pour le client, ce qui se traduit par une meilleure expérience client et une fidélisation accrue. La satisfaction client est ainsi considérée comme un indicateur clé de la réussite des pratiques Lean au sein d’une organisation.
Chapitre 2 : Les Principes et commandements du Lean
Les « principes du Lean » sont définis dans de multiples références du Lean. Par exemple dans la « Maison TPS », le « Lean Thinking » de « Toyota Way 2001», et le «The Toyota Way: 14 Management Principles from the World’s Greatest Manufacturer.»
- Les principes du Lean de la « Maison TPS »
Le célèbre diagramme de la « maison TPS » est la première modélisation du système TPS. Il comporte cinq éléments, ou principes du Lean :
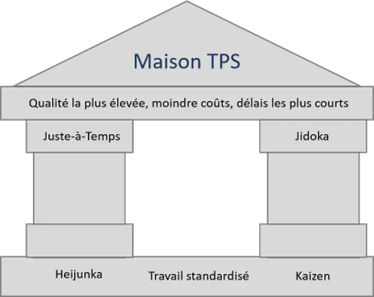
– Une base à trois éléments/principes :
- Heijunka : lissage de la production, en volume ou en mix produit pendant une certaine période, afin de réduire les conséquences de la fabrication purement à la demande
- Travail standardisé : standardisation des procédures afin de favoriser la reproductibilité de la production et l’apprentissage par le personnel
- Kaizen : amélioration continue
– Deux piliers / principes :
- JIT : Juste-à temps
- Jidoka : Souvent traduit par « autonomation » en anglais ou français, il possède deux significations :
- Détacher ou libérer l’humain de la machine (lui permettant d’en superviser plusieurs)
- Ne pas laisser de défauts passer (arrêt de la machine), ce qui crée un système de « Qualité intégré » ou « Bon du premier coup »
-
Les cinq principes du Lean de « Lean Thinking » de Womack, Jones et Roos
Ce sont James P. Womack, Daniel T. Jones, et Daniel Roos qui ont formalisé les premiers le nom et la démarche « Lean » dans leur livre « The Machine That Changed the World » publié en 1991. Ils ont défini cinq principes du Lean dans leur ouvrage suivant, « Lean Thinking » publié en 1996.

2.1.- Identification de la Valeur (Value)
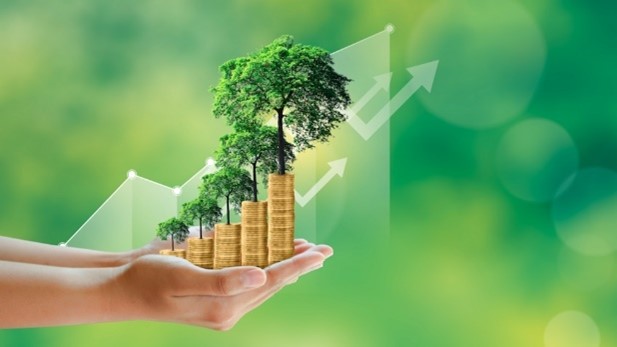
Le premier principe consiste à définir la valeur du point de vue du client. La valeur est déterminée par ce que le client est prêt à payer. Les entreprises doivent comprendre les attentes et les besoins des clients pour orienter leurs activités vers la création de cette valeur.
2.2- Mapping du Flux de Valeur (Value Stream Mapping)
Une fois que la valeur a été identifiée, le deuxième principe implique de cartographier le flux de valeur, c’est-à-dire d’analyser tous les processus nécessaires pour livrer le produit ou le service. Cela permet d’identifier les étapes qui ajoutent de la valeur et celles qui génèrent du gaspillage. L’objectif est d’optimiser le flux pour éliminer les temps morts et les inefficacités.
2.3- Création de Flux Continu (Flow)
Le troisième principe vise à créer un flux continu en éliminant les interruptions et les retards entre les différentes étapes du processus. Cela implique de réorganiser les opérations pour permettre un flux lisse et continu du début à la fin. La production est alignée sur la demande réelle plutôt que sur des prévisions, créant ainsi un flux plus efficace.
2.4- Production Tirée (Pull)
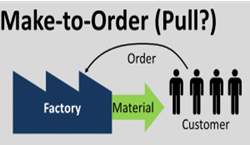
Le principe du « Pull » consiste à produire uniquement ce qui est nécessaire en fonction de la demande réelle. Les produits ou services ne sont pas fabriqués avant d’être requis, ce qui réduit les niveaux de stock et minimise le gaspillage lié à la surproduction. Le Pull crée une réponse rapide aux changements de demande.
2.5- Recherche de la Perfection (Perfection)
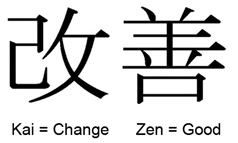
Le cinquième principe du Lean Management, souvent appelé « Kaizen » (amélioration continue), repose sur la recherche constante de la perfection. Les organisations Lean s’engagent dans une amélioration continue de leurs processus, encourageant l’innovation, la résolution proactive des problèmes et l’implication de tous les membres de l’organisation pour créer un environnement d’apprentissage continu.
-
Les deux piliers et les cinq principes du « Toyota Way 2001 »
Dans les années 1990, à la suite d’un déploiement plus généralisé du Lean et à des échecs de mise en œuvre, certaines critiques sont apparues. Le Lean et le « Toyota Production System » semblaient trop techniques sans assez prendre en compte la dimension humaine. Ils étaient plus connus pour les méthodes « Kaizen », « Kanban » ou « travail standardisé » que pour le « respect pour les personnes ». Fuji Cho, président de Toyota de 1999 à 2005, a alors fait publier en 2001 le « Toyota Way 2001 ». Celui-ci décrit officiellement les principes du Lean (les principes du TPS pour Toyota) avec une définition plus conforme à la réalité telle que vécue chez Toyota. Notamment en mettant plus en avant cette dimension humaine qui lui semblait essentielle.
Le « Toyota Way 2001 » décrit cinq principes du Lean, articulés au sein de deux piliers :
– Amélioration continue
- Défis
- Kaizen
- Genchi Genbutsu
– Respect pour les personnes
- Respect
- Travail d’équipe
Le schéma suivant extrait d’un document Toyota explique plus en détail ces principes du Lean
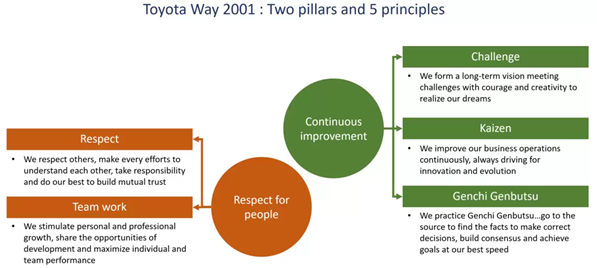
-
«The Toyota Way: 14 Management Principles from the World’s Greatest Manufacturer» by Jeffrey K. Liker
Jeffrey K. Liker est professeur émérite de génie industriel et opérationnel à l’Université du Michigan. Il a écrit de nombreux livres sur Toyota dont celui qui est un Bestseller à plus d’un million de livres. Il a aussi gagné plus de 13 Prix Shingo d’Excellence de recherche. Dans « The Toyota Way: 14 Management Principles from the World’s Greatest Manufacturer » il identifie les 14 principes de management de Toyota, dont certains sont déjà exposés.
Ces principes de management contiennent certains principes du Lean déjà évoqués auparavant :
Première partie : Philosophie à long terme
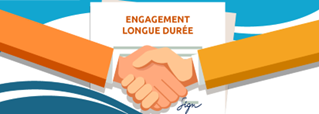
Principe 1 – Fonder vos décisions de management sur une philosophie à long terme, même au détriment des objectifs financiers à court terme.
Deuxième partie : Les bons processus produiront les bons résultats

- Principe 2 – Créer un flux de processus continu pour faire remonter les problèmes à la surface. (Juste à temps)
- Principe 3 – Utiliser des systèmes de traction pour éviter la » surproduction « .
- Principe 4 – Égaliser la charge de travail. (Éliminer l’attente)
- Principe 5 – Bâtir une culture de » l’arrêt pour régler les problèmes » afin d’assurer la qualité. (Éliminer les retouches)
- Principe 6 – Les tâches standardisées sont le fondement de l’amélioration continue et de la responsabilisation des employés.
- Principe 7 – Utiliser des contrôles visuels pour ne cacher aucun problème. (Les opportunités sont visibles pour tous)
- Principe 8 – N’utilisez que des technologies fiables et soigneusement testées au service de votre personnel et de vos processus.
Troisième partie : Ajouter de la valeur à l’organisation par le développement vos employés et les partenaires
- Principe 9 – Former des leaders qui comprennent parfaitement le travail, vivent la philosophie et l’enseignent aux autres.
- Principe 10 – Former des personnes et des équipes exceptionnelles qui suivent la philosophie de votre entreprise.
- Principe 11 – Respectez votre réseau élargi de partenaires et de fournisseurs en les remettant en question et en les aidant à s’améliorer.
Quatrième partie : Résoudre les problèmes racines en continu génère l’apprentissage de l’organisation
- Principe 12 – Allez voir par vous-même et comprenez bien la situation.
- Principe 13 – Prendre des décisions lentement par consensus, en examinant à fond toutes les options, puis les mettre en œuvre rapidement.
- Principe 14 – Devenir une organisation apprenante par une réflexion constante et une amélioration continue
-
Les 10 commandements du Lean
5.1- Débarrassez-vous du concept traditionnel des méthodes de production
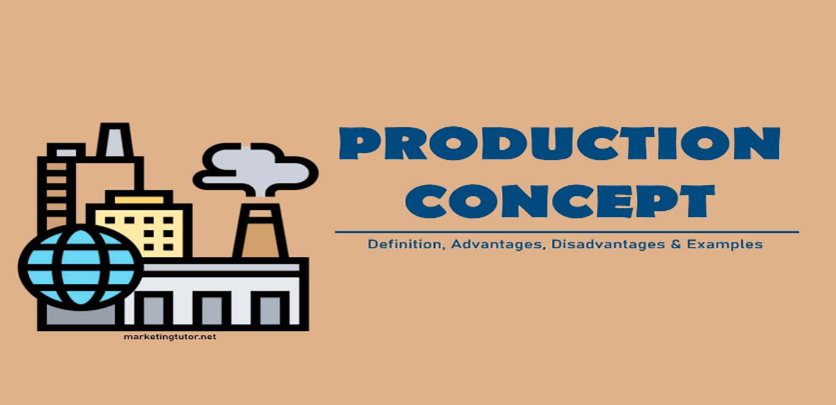
Rejetez les approches conventionnelles et remettez en question les méthodes établies. Le Lean encourage à repenser les processus et à adopter une approche plus efficace et efficiente.
5.2- Voyez comment réussir un projet plutôt que dire cela ne fonctionne pas
Focalisez-vous sur les solutions plutôt que sur les problèmes. Plutôt que de déclarer qu’une idée ne fonctionne pas, cherchez des moyens de la faire fonctionner en identifiant des approches alternatives et des améliorations.
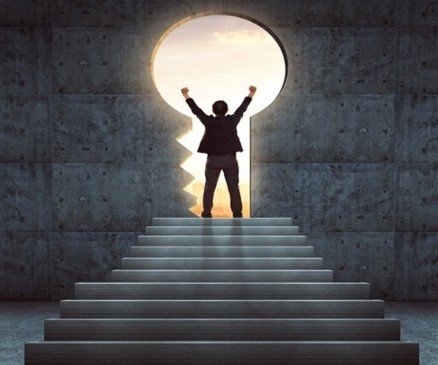
5.3- N’acceptez pas les excuses. Refusez le statut actuel
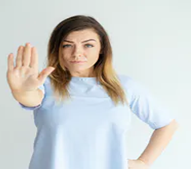
Le Lean encourage à refuser la complaisance et à ne pas accepter le statu quo. Évitez les excuses et cherchez constamment des opportunités d’amélioration.
5.4- Ne cherchez pas la perfection du 1er coup mais cherchez simplement l’amélioration
Évitez de viser la perfection immédiate. Priorisez plutôt des améliorations progressives. L’objectif est de créer une culture d’amélioration continue où les petites améliorations s’accumulent au fil du temps.

5.5- Corrigez les erreurs dès qu’elles apparaissent

Lorsqu’une erreur survient, agissez rapidement pour la corriger. Cette approche préventive permet d’éviter que des problèmes mineurs ne deviennent des problèmes majeurs.
5.6- Priorisez des améliorations à faibles investissements
Donnez la priorité aux changements qui apportent une grande valeur avec des investissements minimes. Cela encourage une approche pragmatique et économique pour maximiser les avantages.
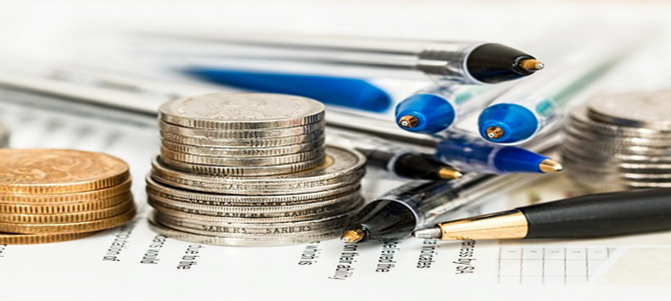
5.7- Même si cela fonctionne bien, cherchez l’amélioration
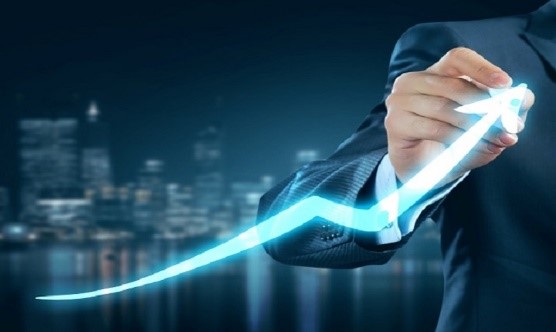
Le Lean ne se contente pas de maintenir le statu quo, même si les choses semblent bien fonctionner. Il encourage la recherche constante d’améliorations, même dans les processus apparemment efficaces.
5.8- Posez la question « Pourquoi ? » 5 fois pour chercher la cause réelle
La méthode des « 5 Pourquoi » est une technique qui consiste à poser la question « Pourquoi ? » de manière itérative jusqu’à ce que la cause fondamentale d’un problème soit identifiée. Cela favorise une compréhension approfondie des problèmes et des solutions durables.

5.9- Les idées de 10 personnes sont meilleures que les idées d’1 seule personne

Encouragez la collaboration et la diversité d’idées. En impliquant plusieurs perspectives, vous augmentez les chances de générer des solutions créatives et innovantes.
5.10- L’amélioration n’a pas de limites
Le Lean Management embrasse le concept que l’amélioration est un processus continu et sans fin. Il n’y a pas de limite à la recherche de meilleures façons de faire les choses, et chaque étape vers l’amélioration contribue à renforcer l’efficacité globale.

Ces commandements du Lean réaffirment l’importance de l’amélioration continue, de la flexibilité mentale, et de la recherche constante de solutions créatives dans le contexte du Lean Management.
-
Les types de gaspillages (muda)
6.1- Gaspillages provenant de la surproduction

C’est à dire produire plus rapidement que la demande du client, et ainsi gaspiller en avance de la matière, de l’espace de stockage (locaux et surfaces utilisés, coûts assurances, gardiennage), des moyens de manutention, de l’énergie humaine et tout en prenant le risque d’avoir des obsolètes.
=> Porter une grande attention à la planification mais aussi accepter de ne pas chercher le plein emploi des ressources (TAKT TIME). Dans le but de produire uniquement les quantités nécessaires et de ne pas créer d’inventaire, il convient de déterminer la quantité de produits à fabriquer qui répondra exactement aux besoins des clients.
6.2- Gaspillages provenant des temps d’attente
Les arrêts non désirés de la chaine de production deviennent extrêmement critiques pour le respect des délais de livraison.
• J’attends des ordres de fabrication (OF)
• J’attends l’outillage
• J’attends la matière première
• J’attends la production de l’atelier amont
• J’attends la qualité
=> Organisation
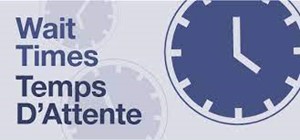
6.3- Gaspillages provenant des Transports
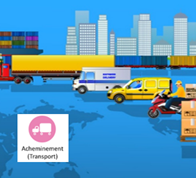
Tout mouvement de produit ou de matériel sans création de valeur ajoutée est considéré comme une source de gaspillage.
Bien que la considération du transport comme étant une source du gaspillage soit conditionnée par le non-apport de valeur ajoutée, cette condition est souvent vraie.
Le transport pourrait être d’un département à un autre dans une même usine, comme il peut être entre deux usines dans deux pays éloignés. L’essentiel, est que le transport est une source de charge pour laquelle le client final n’est pas censé payer, ce qui génère inévitablement une perte, soit au niveau des coûts d’opération, soit en termes de compétitivité, et dans le pire des cas, pour les deux.
Solution : Placer les différentes ressources très près les unes des autres dans des lieux propres et rangés (5S) :
• Réduit les besoins de transport
• Et interdit physiquement de gros inter stocks (juste la quantité suffisante : KANBAN en production)
• Effectuer les différentes opérations dans le même poste
=>Afin d’éliminer ces pertes, il est nécessaire d’assurer un aménagement optimal.
6.4- Processus inutiles
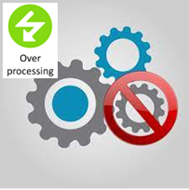
Le gaspillage lié au processus inutile (Overprocessing) dans le contexte du Lean Management se réfère à l’accomplissement d’activités ou d’étapes qui n’ajoutent pas de valeur au produit final du point de vue du client.
Cela signifie que certaines étapes du processus de production, de service ou de développement sont excessives par rapport aux besoins ou aux attentes du client, entraînant un gaspillage de ressources telles que le temps, la main-d’œuvre et les matériaux. Voici quelques points de développement sur le processus inutile :
Redondance d’étapes : Les étapes redondantes qui ne contribuent pas directement à la qualité ou à la fonctionnalité du produit final peuvent être sources de gaspillage.


Trop de contrôles de qualité : Des contrôles de qualité excessifs ou des tests répétitifs au sein du processus peuvent être considérés comme du surtraitement s’ils dépassent les normes nécessaires pour garantir la qualité du produit.
Spécifications dépassées : Parfois, les produits sont fabriqués selon des spécifications dépassées ou des normes de qualité plus strictes cela peut entraîner une utilisation excessive de ressources.
Documentation excessive : Un excès de documentation, de rapports ou de procédures peut être considéré comme du surtraitement s’il n’apporte pas de valeur ajoutée directe au produit ou au service.

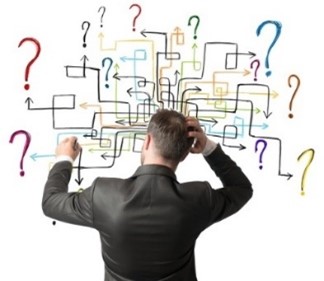
Complexité inutile : Les processus trop complexes, avec des étapes inutiles ou des structures compliquées, peuvent entraîner une perte de temps et d’énergie sans amélioration significative de la qualité du produit.
Surcharges administratives : Des processus administratifs complexes, des autorisations excessives ou des approbations multiples peuvent ajouter des délais inutiles et augmenter la charge de travail sans valeur ajoutée.
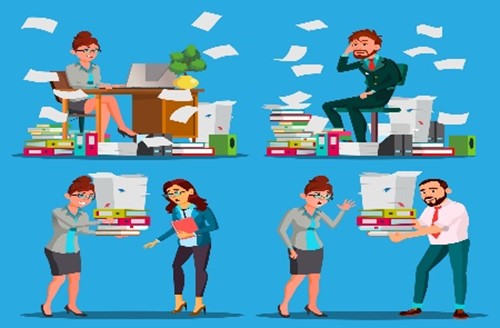
=> L’objectif du Lean Management est d’optimiser les processus en éliminant ces activités inutiles afin de réduire les coûts, d’améliorer l’efficacité et de fournir un produit ou un service de qualité au client. Cela implique souvent la
6.5- Gaspillages provenant des stocks
Le stock inutile (Excess Inventory) peut entraîner plusieurs conséquences négatives sur une entreprise, et le Lean Management cherche à le minimiser autant que possible. Voici quelques gaspillages provenant des stocks :
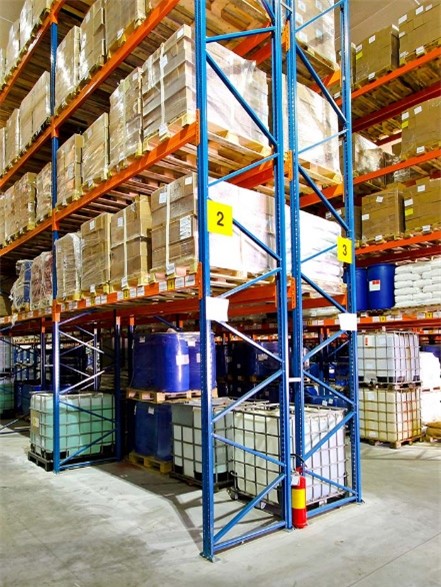
Coûts de stockage : La détention d’un stock excessif implique souvent des coûts de stockage élevés. Les entreprises doivent payer pour l’espace de stockage, la sécurité, …
Obsolescence : Les produits en stock peuvent devenir obsolètes, ils peuvent perdre de la valeur, nécessitant des rabais, des promotions spéciales ou même des pertes.
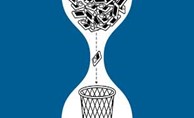
Risques financiers : Les stocks excessifs représentent un investissement financier important. Si la demande diminue ou si les produits deviennent obsolètes, l’entreprise risque de subir des pertes financières importantes.
Manque de flexibilité : L’argent investi dans le stock inutile pourrait être utilisé de manière plus flexible pour répondre rapidement aux demandes changeantes des clients.

Complexité de gestion : La gestion d’un inventaire excessif est souvent complexe. Il peut être difficile de suivre tous les articles stockés, de prévenir les ruptures de stock et de minimiser les coûts associés à la gestion de cet inventaire.
=> Le Management encourage la mise en place de systèmes de production tirée (pull systems), où la production est basée sur la demande réelle plutôt que sur des prévisions. Les entreprises Lean travaillent souvent à améliorer la visibilité de la chaîne d’approvisionnement et à mettre en place des mécanismes pour produire juste à temps (Just-In-Time), ce qui réduit les coûts liés au stock inutile tout en répondant efficacement à la demande du client.
6.6- Gaspillages provenant des mouvements inutiles

Le gaspillage lié au « Mouvement inutile » (Unnecessary Motion) dans le cadre du Lean Management se réfère aux mouvements physiques superflus effectués par les travailleurs, les machines ou les équipements au sein d’un processus de production ou d’un environnement de travail.
Cela englobe tout déplacement qui n’ajoute pas de valeur au produit ou au service, mais qui peut entraîner une fatigue accrue, des erreurs et une perte de temps. Dans la suite quelques aspects à considérer en ce qui concerne les mouvements inutiles :
Disposition inefficace des équipements : Si les machines, les outils ou les postes de travail ne sont pas agencés de manière logique, les travailleurs peuvent être obligés de se déplacer inutilement pour accéder à des ressources ou effectuer des tâches.

Recherche d’outils ou de matériaux : Des mouvements inutiles peuvent survenir lorsque les travailleurs doivent constamment chercher des outils, des pièces ou des matériaux nécessaires à leur tâche. Une organisation inefficace peut entraîner des déplacements inutiles.
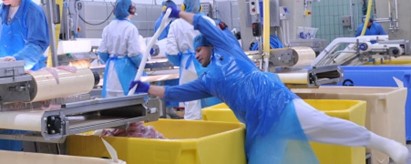
Mauvaise ergonomie : Des conditions de travail peu ergonomiques peuvent obliger les travailleurs à adopter des postures ou des gestes qui nécessitent des mouvements excessifs, et inutiles.
Transferts de matériaux inutiles : Des déplacements excessifs de matériaux ou de produits entre différentes zones de travail peuvent ajouter du temps non productif au processus de production.
Attentes inutiles : Si les travailleurs doivent attendre que d’autres tâches soient terminées ou que des matériaux soient disponibles, cela peut entraîner des mouvements inutiles ou des déplacements qui ne contribuent pas à la valeur du produit.
Transport inefficace de l’information : Des processus de communication inutiles ou des déplacements excessifs pour partager des informations peuvent entraîner des retards et une perte d’efficacité.
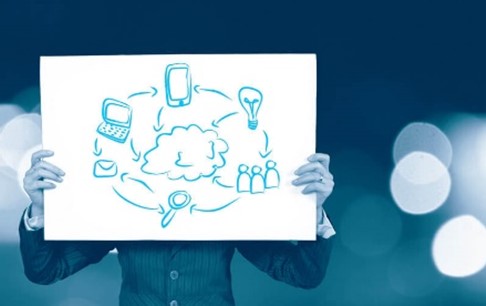
=> Pour éliminer le gaspillage lié au mouvement inutile, les entreprises Lean cherchent à concevoir des environnements de travail ergonomiques, à organiser les flux de travail de manière logique et à minimiser les déplacements non productifs. En optimisant la disposition et en éliminant les sources de mouvement inutile, les organisations peuvent améliorer l’efficacité, réduire la fatigue des travailleurs et augmenter la productivité globale.
6.7- Gaspillages provenant des défauts
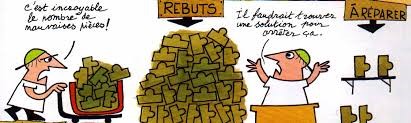
La notion de « Défauts » (Defects) dans le contexte du Lean Management se réfère à la production de produits ou de services qui ne répondent pas aux normes de qualité ou aux attentes du client. La philosophie Lean vise à minimiser, voire éliminer, la production de défauts pour garantir une qualité optimale et satisfaire pleinement les besoins des clients. Voici quelques inconvénients dus aux gaspillages provenant défauts :
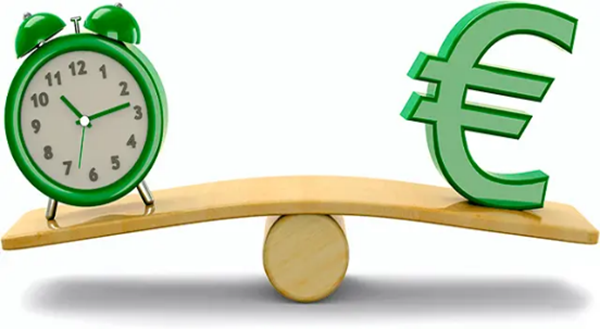
Coûts de correction : La correction des défauts peut être une tâche coûteuse en termes de main-d’œuvre, de temps et de matériaux. Les entreprises doivent souvent investir des ressources supplémentaires pour réparer ou remanufacturer les produits défectueux.
Insatisfaction client : Les défauts entraînent généralement une insatisfaction client. Les clients s’attendent à recevoir des produits ou des services de qualité, et des défauts peuvent compromettre la réputation de l’entreprise et entraîner des retours, des remplacements ou des remboursements.

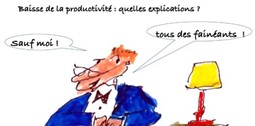
Perte de productivité : La production de défauts peut entraîner des interruptions dans le processus de production, car il faut souvent arrêter les opérations normales pour corriger les erreurs, ce qui peut entraîner une perte de productivité.
Coûts liés aux retours : Les produits défectueux peuvent être retournés par les clients, ce qui entraîne des coûts supplémentaires liés au traitement des retours, au remplacement des produits et à la gestion des relations avec les clients mécontents.
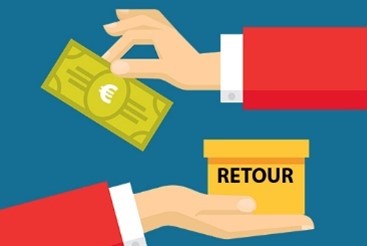
=> La démarche Lean vise à éliminer la source des défauts plutôt que de simplement corriger les erreurs après leur apparition. Cela implique la mise en place de méthodes telles que le contrôle de la qualité en amont, la formation des employés, l’utilisation d’outils de résolution de problèmes et l’adoption d’une culture d’amélioration continue (Kaizen). En investissant dans la prévention des défauts plutôt que dans la correction, les entreprises peuvent réduire les coûts liés à la non-qualité, améliorer la satisfaction client et renforcer leur réputation sur le marché.
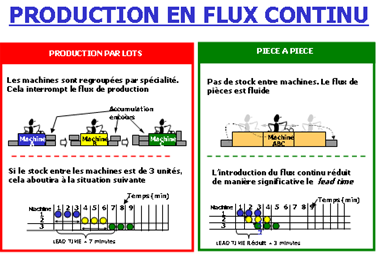
Le concept de flux continu, ancré dans les principes du Lean Management, représente une méthodologie essentielle visant à optimiser les processus de travail. Il s’agit de créer des flux de travail sans interruption, assurant une efficacité maximale tout en mettant l’accent sur la valeur ajoutée pour le client. Pour illustrer ce concept, prenons l’exemple d’une chaîne de production dans une usine automobile. En adoptant le flux continu, chaque étape du processus est minutieusement synchronisée, éliminant ainsi les temps d’attente entre les différentes phases de production. Cela permet non seulement de réduire les délais, mais aussi de minimiser les stocks inutiles, car la production est alignée sur la demande réelle.
Un autre exemple concret pourrait être celui d’une entreprise de logistique qui applique le concept de flux continu dans la gestion des commandes. En évitant les arrêts inutiles et en éliminant les tâches non essentielles, l’entreprise peut accélérer le traitement des commandes et répondre plus rapidement aux besoins des clients. De plus, en réduisant les retards potentiels et en maintenant un flux constant, les coûts liés au stockage excessif diminuent, contribuant ainsi à une utilisation plus efficace des ressources.
En résumé, le concept de flux continu se matérialise par des processus optimisés, réduisant le gaspillage, les délais et les coûts superflus. Que ce soit dans la fabrication, la logistique ou d’autres domaines, l’application de ce principe du Lean Management se traduit par une amélioration significative de l’efficacité opérationnelle et de la satisfaction client.
Chapitre 4 : Amélioration Continue et Kaizen
1.Amélioration continue VS Kaizen
1.1- Amélioration Continue
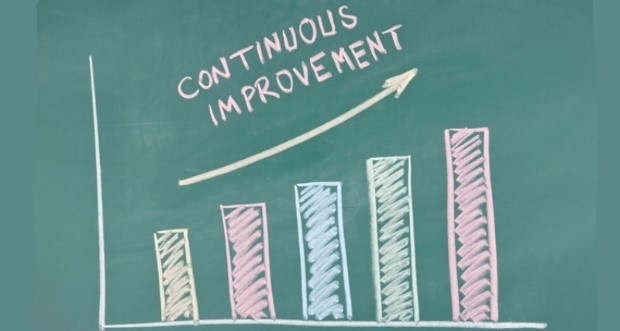
Philosophie Générale
L’Amélioration Continue est une philosophie qui vise à constamment améliorer les processus, les produits ou les services d’une organisation.
Approche Systématique
Elle adopte une approche systématique pour identifier, analyser et éliminer les inefficacités, les gaspillages et les problèmes.
Mentalité Proactive
L’Amélioration Continue encourage une mentalité proactive, incitant à rechercher constamment des opportunités d’amélioration.
1.2- Kaizen

Origine Japonaise
Kaizen est un terme japonais qui signifie « changement » (kai) « pour le mieux » (zen).
Méthode Spécifique
Le Kaizen est une méthode spécifique d’Amélioration Continue qui se concentre sur des petites améliorations continues et incrémentales dans les processus.
Implémentation Continue
Il met l’accent sur l’implémentation continue de petites améliorations au quotidien, impliquant l’ensemble de l’organisation.
Participation de Tous
Kaizen encourage la participation de tous les membres de l’organisation, de la direction aux travailleurs de première ligne, dans le processus d’amélioration.
=> En résumé, l’Amélioration Continue est une philosophie plus large englobant la quête constante de l’excellence opérationnelle, tandis que le Kaizen est une méthode spécifique d’Amélioration Continue axée sur des améliorations continues et incrémentales, avec une participation active de tous les membres de l’organisation. Le Kaizen est souvent considéré comme une application concrète de la philosophie plus vaste de l’Amélioration Continue.
L’Amélioration Continue et le Kaizen sont des concepts clés dans le domaine du management, en particulier dans le contexte de la gestion de la qualité et de l’efficacité opérationnelle.
2.Les principes clés de Kaizen
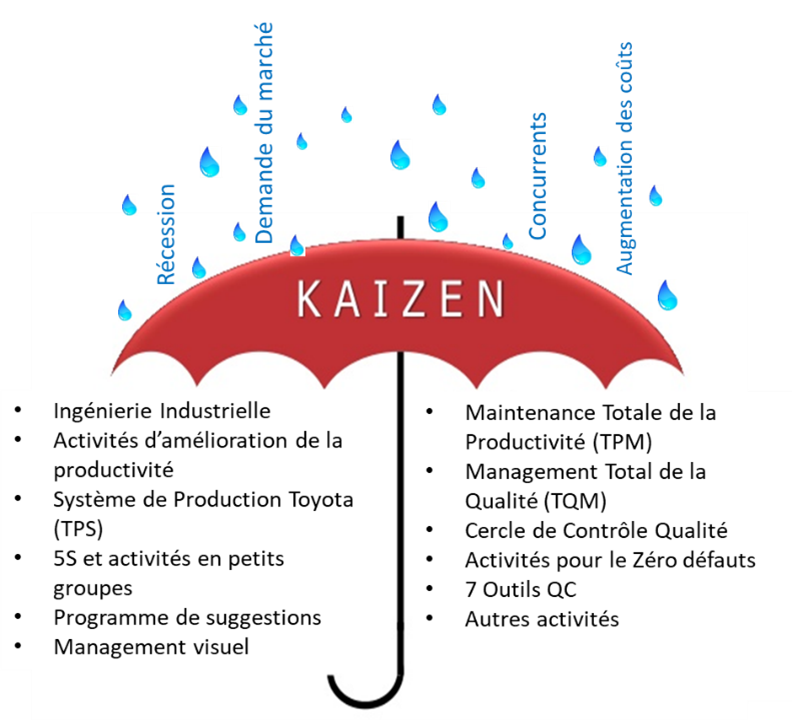
2.1- Total Quality Management (TQM)
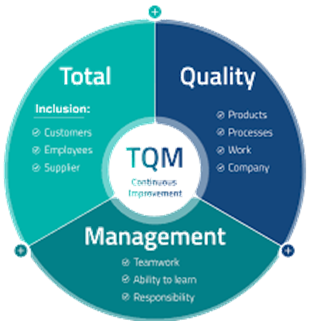
Le TQM (Total Quality Management – Gestion de la Qualité Totale) est une approche de gestion qui vise à intégrer tous les processus et fonctions d’une organisation pour atteindre l’amélioration continue de la qualité.
Les principes clés du TQM incluent l’implication de tous les membres de l’organisation, l’orientation client, la prise de décision basée sur des faits et données, et l’accent mis sur la prévention des problèmes plutôt que sur leur correction. Le TQM vise à créer une culture d’amélioration continue de la qualité dans toute l’entreprise.
2.2- Toyota Production System (TPS)
Le TPS (Toyota Production System – Système de Production Toyota), développé par Toyota, est un système de production qui met l’accent sur l’élimination des gaspillages et l’amélioration continue. Il est connu pour ses principes tels que le Juste-à-Temps (JIT), la production au plus bas coût, et le respect des personnes.
Le TPS vise à produire des biens de haute qualité de manière efficace tout en minimisant les stocks, les délais et les coûts. Il a influencé de manière significative les concepts modernes de gestion et est souvent associé aux principes du Lean Manufacturing.
2.3- Total Productive Maintenance (TPM)
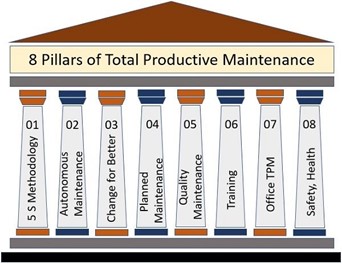
Le TPM (Total Productive Maintenance – Maintenance Productive Totale) est une approche de gestion qui se concentre sur la maintenance proactive des équipements pour maximiser leur efficacité et minimiser les temps d’arrêt. L’objectif du TPM est d’impliquer l’ensemble de l’organisation dans la maintenance et l’amélioration des équipements. Il s’agit de prévenir les pannes, d’optimiser les cycles de vie des équipements et d’assurer une production sans heurts.
Le TPM met l’accent sur l’autonomisation des opérateurs et la création d’une culture où la maintenance est la responsabilité de tous.
2.4- Cercles de contrôle qualité
Le terme « cercle de contrôle qualité » fait référence à une pratique spécifique d’amélioration continue qui implique la formation d’un groupe de travailleurs au sein d’une organisation, souvent issus du même département ou de la même équipe, pour résoudre des problèmes de qualité spécifiques.
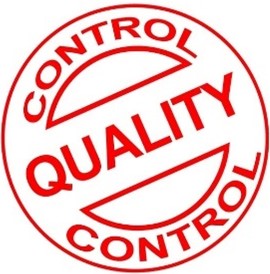
Cette approche a été popularisée au Japon dans les années 1960 et est également connue sous le nom de « Cercle de Qualité » ou « Cercle de Kaizen ».
Les principales caractéristiques et éléments associés au cercle de contrôle qualité :
1/ Formation de Groupes
Les membres du cercle de contrôle qualité sont des employés travaillant sur des tâches similaires ou dans le même secteur de l’organisation. Ces groupes sont souvent autonomes et ont pour mission de résoudre des problèmes de qualité spécifiques.
2/ Objectif d’Amélioration Continue
Le principal objectif du cercle de contrôle qualité est d’identifier, d’analyser et de résoudre les problèmes de qualité au sein de leur domaine d’activité. Ils travaillent constamment à améliorer les processus, à réduire les défauts et à accroître l’efficacité opérationnelle.
3/ Utilisation d’Outils de Résolution de Problèmes
Les cercles de contrôle qualité utilisent souvent des outils d’amélioration continue tels que le diagramme d’Ishikawa (ou diagramme de causes et effets), les 5 Pourquoi, les histogrammes, et d’autres méthodes d’analyse de la qualité.
4/ Réunions Régulières
Les membres du cercle se réunissent régulièrement pour discuter des problèmes, des progrès réalisés et des solutions proposées. Ces réunions permettent un échange continu d’idées et de bonnes pratiques.
5/ Participation Active des Membres
Chaque membre du cercle est encouragé à participer activement à la résolution des problèmes. Cela favorise un sentiment de responsabilité partagée et d’engagement envers l’amélioration continue.
6/ Rétroaction et Reconnaissance
Les résultats obtenus grâce aux efforts du cercle de contrôle qualité sont évalués, et les membres sont reconnus pour leurs contributions. La rétroaction constructive est utilisée pour ajuster les approches et optimiser les résultats.
Le cercle de contrôle qualité s’inscrit dans la philosophie d’amélioration continue, encourageant l’implication des employés à tous les niveaux de l’organisation pour créer une culture d’excellence opérationnelle.
3. Implémentation de Kaizen dans les processus
L’implémentation de Kaizen dans les processus nécessite une approche structurée et une compréhension profonde des principes de Kaizen. Les étapes clés pour mettre en œuvre Kaizen dans les processus de manière effective sont :
1/ Créer une Culture Kaizen
Faire comprendre l’importance de l’amélioration continue et comment elle contribue à la réussite globale de l’entreprise. Encourager la mentalité de Kaizen à tous les niveaux hiérarchiques.
2/ Établir des Objectifs Clairs
Définir des objectifs spécifiques et réalisables pour chaque processus à améliorer. Les objectifs doivent être alignés sur les priorités stratégiques de l’entreprise.
3/ Identifier les Points d’Amélioration
Impliquer les employés directement concernés par le processus dans l’identification des opportunités d’amélioration. Utiliser des méthodes telles que les flux de valeur (Value Stream Mapping) pour visualiser le processus actuel.
4/ Encourager la Participation de Tous
Impliquer tous les membres de l’équipe, quel que soit leur niveau hiérarchique, dans la génération d’idées et la mise en œuvre de changements.
Favoriser un environnement où chacun se sent à l’aise de partager ses observations et suggestions.
5/ Mettre en Place des Équipes Kaizen
Créer des équipes Kaizen composées de membres de différentes fonctions et niveaux de l’organisation. Ces équipes sont responsables de la mise en œuvre des améliorations identifiées.
6/ Utiliser des Outils Kaizen
Appliquer des outils spécifiques tels que le 5 Pourquoi, le Kanban, les 5S, etc., selon les besoins du processus. Utiliser des méthodes PDCA pour planifier, exécuter, vérifier et ajuster.
7/ Mettre en Œuvre des Changements Graduels
Privilégier des changements progressifs et mesurables plutôt que des transformations radicales. Tester les changements sur une petite échelle avant de les déployer à grande échelle.
8/ Assurer un Suivi et une Évaluation Continus
Établir des mécanismes de suivi pour évaluer l’impact des changements. Collecter des données pour mesurer la performance avant et après les améliorations.
9/ Célébrer les Réussites et Encourager la Persévérance
Reconnaître et célébrer les succès obtenus grâce à l’implémentation de Kaizen. Encourager la persévérance en soulignant que l’amélioration continue est un processus continu.
10/ Réitérer et S’Adapter
Kaizen est un processus cyclique. Réitérer le cycle PDCA pour continuer à identifier de nouvelles opportunités d’amélioration.
Chapitre 5 : Lean dans les Services et les Entreprises
Le Lean, initialement développé dans le contexte de la fabrication et de la production, a été étendu avec succès aux services et aux entreprises. Le principe fondamental du Lean Management consiste à éliminer le gaspillage tout en optimisant l’efficacité et en maximisant la valeur pour le client.
1. Adaptation du Lean aux services
Le Lean dans les services s’est montré particulièrement efficace dans des domaines tels que la santé, la finance, l’éducation, l’informatique, les télécommunications, et bien d’autres. Les principes Lean peuvent être adaptés à divers environnements et contribuent à améliorer l’efficacité opérationnelle tout en répondant aux attentes des clients. L’adaptation du Lean aux services, souvent appelée le « Lean Services » ou le « Lean Thinking for Services », consiste à appliquer les principes et les techniques du Lean Management dans les entreprises de services plutôt que dans les contextes de fabrication. L’objectif reste le même : éliminer le gaspillage, optimiser les processus et maximiser la valeur pour le client. Voici comment le Lean est adapté aux services :
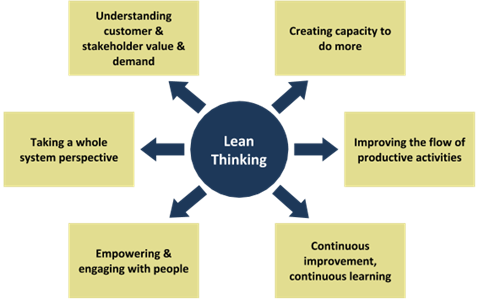
1.1- Identification des Valeurs Clients
Dans le contexte du Lean appliqué aux services, l’identification des valeurs clients revêt une importance cruciale. Il s’agit de comprendre les attentes spécifiques, les besoins, et les priorités des clients, de manière à orienter toutes les activités de services vers la création de valeur. Cette étape initiale permet d’assurer que les efforts sont concentrés sur la prestation de services qui répondent véritablement aux exigences des clients, contribuant ainsi à une satisfaction client accrue.
1.2- Analyse des Flux de Travail
L’analyse des flux de travail dans les services va au-delà de la simple identification des étapes inutiles. Elle vise à détecter les goulots d’étranglement, les retards potentiels, et toute forme de gaspillage pouvant entraver la fluidité du processus. En simplifiant les processus et en optimisant la séquence des activités, les entreprises de services peuvent non seulement améliorer l’efficacité opérationnelle mais également offrir des services de meilleure qualité dans des délais plus courts.
1.3- Production Tirée
L’application du principe de production tirée dans les services révolutionne la manière dont les services sont fournis. Plutôt que de se baser sur des prévisions, les entreprises répondent directement à la demande réelle des clients. Cela signifie que les services sont délivrés au moment précis où le client en exprime le besoin, réduisant ainsi les délais et maximisant la pertinence des services fournis.

1.4- Gestion Visuelle
La gestion visuelle est un pilier du Lean dans les services, utilisant des outils tels que les tableaux Kanban et les diagrammes de flux pour rendre les processus transparents. En visualisant le flux de travail, les équipes peuvent rapidement identifier les problèmes, suivre les progrès et prendre des décisions éclairées. Cela favorise une compréhension commune des processus au sein de l’équipe, facilitant la collaboration et la résolution collective des problèmes.
1.5- Systèmes Juste-à-Temps (JIT)
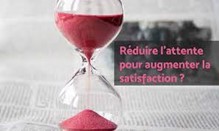
L’introduction de systèmes Juste-à-Temps dans les services vise à minimiser les temps d’attente et à réduire les délais en alignant la prestation des services sur la demande réelle des clients. Cela permet d’éviter la surproduction de services et contribue à une utilisation plus efficace des ressources, renforçant ainsi l’efficacité globale des processus de services.
1.6- Flexibilité des Employés
Dans un environnement Lean, la flexibilité des employés est cruciale. Les équipes sont formées pour être polyvalentes, capables d’accomplir différentes tâches en fonction des besoins. Cette flexibilité renforce la capacité de s’adapter aux fluctuations de la demande, assurant ainsi une utilisation optimale des compétences et une réactivité accrue aux changements.
1.7- Amélioration Continue (Kaizen)
Le Lean dans les services promeut activement une culture d’amélioration continue, inspirée du concept japonais Kaizen. Les employés sont encouragés à identifier constamment des opportunités d’amélioration, à tester de nouvelles idées, et à participer activement à la résolution des problèmes. Cela crée un environnement dynamique où l’innovation et l’amélioration sont des processus constants.
1.8- Gestion de la Complexité
La gestion de la complexité dans les services implique la simplification et la rationalisation des offres. En éliminant les options ou les caractéristiques qui n’ajoutent pas de valeur significative pour le client, les entreprises de services visent à créer des offres claires, cohérentes et plus faciles à gérer.
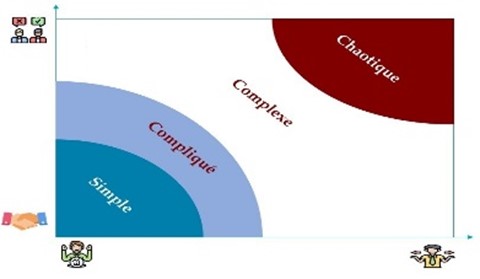
1.9- Mesure et Analyse des Performances
La mise en place de mesures de performances dans le cadre du Lean dans les services est essentielle pour suivre la productivité, la qualité des services, les délais, et d’autres indicateurs clés. Cette analyse constante des performances permet de prendre des décisions éclairées pour optimiser les processus et améliorer l’efficacité opérationnelle.
1.10- Communication et Collaboration
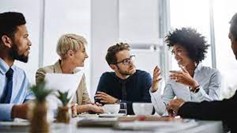
Une communication efficace et une collaboration étroite entre les équipes sont au cœur du Lean dans les services. Encourager les équipes de services à travailler ensemble pour résoudre les problèmes et améliorer les processus crée un environnement où les connaissances sont partagées, les idées sont discutées, et les solutions sont élaborées de manière collective, favorisant ainsi une culture de l’efficacité collective.
L’adaptation du Lean aux services nécessite souvent une approche spécifique en raison des différences inhérentes entre la fabrication et les services. Cependant, les principes fondamentaux du Lean peuvent être appliqués avec succès pour améliorer l’efficacité opérationnelle, la qualité des services et la satisfaction client dans divers secteurs de services.
2.Application du Lean dans les entreprises non manufacturières
L’application du Lean dans les entreprises non manufacturières, également connu sous le nom de Lean Services, est une pratique de plus en plus répandue. Les principes Lean, originellement développés dans le secteur manufacturier, peuvent être adaptés de manière efficace pour améliorer l’efficacité opérationnelle et la qualité des services dans divers secteurs.
2.1- Soins de Santé
Les organisations de soins de santé ont adopté le Lean pour améliorer la qualité des soins, réduire les temps d’attente, et optimiser les processus. Par exemple, des hôpitaux ont mis en place des initiatives Kaizen pour optimiser les flux de travail, réduire les erreurs médicales, et améliorer la satisfaction des patients.
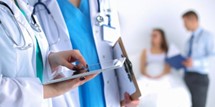
2.2- Services Financiers
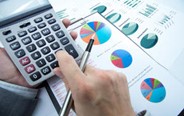
Les institutions financières ont appliqué le Lean pour améliorer l’efficacité de leurs processus, réduire les délais de traitement des demandes de services financiers, et minimiser les erreurs. Cela peut également inclure l’optimisation des processus de back-office tels que le traitement des prêts, la gestion des comptes, etc.
2.3- Éducation
Les établissements éducatifs ont utilisé le Lean pour améliorer les processus d’inscription, réduire les temps d’attente pour les étudiants, et optimiser la planification des cours. Des principes Lean peuvent également être appliqués pour améliorer la gestion des ressources éducatives et la prestation des cours.
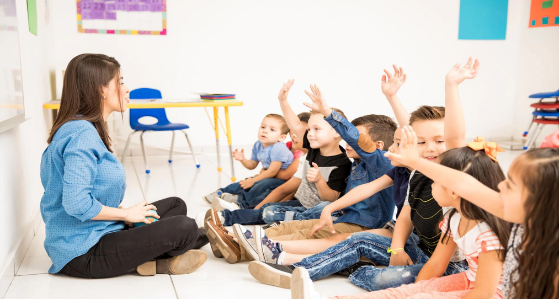
2.4- Services Informatiques et Technologiques
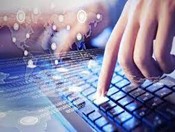
Les entreprises offrant des services informatiques ont adopté le Lean pour optimiser les processus de développement logiciel, réduire les temps de livraison des projets, et améliorer la qualité des produits. Les principes Lean sont également appliqués dans la gestion des services informatiques (ITIL) pour maximiser la valeur pour les utilisateurs finaux.
2.5- Restauration et Hôtellerie
Les entreprises dans le secteur de la restauration et de l’hôtellerie ont appliqué le Lean pour optimiser les processus de service, réduire les temps d’attente des clients, et améliorer la satisfaction client.
Des concepts tels que le JIT (Juste-à-Temps) sont utilisés pour minimiser le gaspillage alimentaire et optimiser la gestion des stocks.
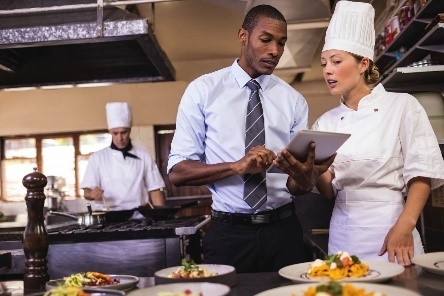
2.6- Administration Publique

Les administrations publiques ont commencé à appliquer le Lean pour améliorer l’efficacité des services publics. Cela peut inclure l’optimisation des processus administratifs, la réduction des temps d’attente pour les services gouvernementaux, et l’amélioration de la transparence.
2.7- Services Logistiques et de Transport
Les entreprises de logistique et de transport ont utilisé le Lean pour optimiser les opérations de gestion des stocks, réduire les temps de transit, et minimiser les coûts d’exploitation. L’accent est mis sur la fourniture de services logistiques de manière efficace et juste à temps.
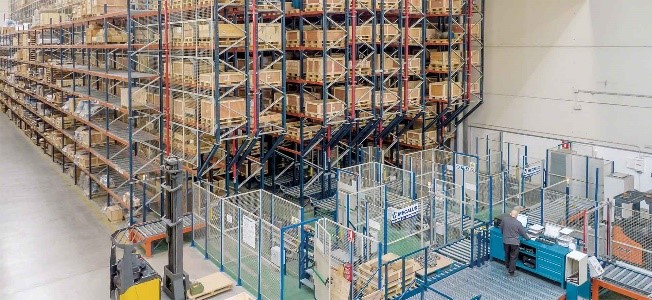
2.8- Services de Consultation et de Conseil
Les entreprises de services de consultation ont adopté le Lean pour optimiser les processus de prestation de services, réduire les délais de livraison des projets, et maximiser la valeur ajoutée pour leurs clients.
=> L’application du Lean dans les entreprises non manufacturières repose sur l’identification des processus clés, l’analyse des flux de travail, et la mise en œuvre d’initiatives d’amélioration continue. La flexibilité et l’adaptabilité des principes Lean permettent une application réussie dans une variété de secteurs de services.
3.Études de cas et exemples pratiques
3.1- Exemple 1 : Parcours de soins dans un hôpital
Pour certains symptômes, les patients sont amenés à rencontrer différents soignants, à réaliser différents examens à l’hôpital, différents actes d’imagerie, afin d’obtenir un diagnostic fiable et une proposition de soins adaptée. Ce processus peut faire l’objet d’une analyse et d’une amélioration à l’aide du Lean.

Nous avons ici :
Processus analysé : Le parcours de soins du patient
Objet suivi dans le processus (par exemple dans le cadre d’une VSM) Le patient
Dans le processus optimisé : Le patient rencontre de manière successive dans une même demi-journée les différents intervenants, les images et/ou prélèvements sont analysés immédiatement, et le patient connaît son diagnostic ainsi que le traitement proposé au moment de quitter l’hôpital.
Dans le processus non optimisé
Le patient doit lui-même prendre rendez-vous avec chaque spécialiste, patienter plusieurs semaines entre deux examens successifs, transférer lui-même les résultats d’un examen chez le praticien suivant. On peut imaginer le stress et les désagréments que connaît le patient dans ce cas de figure.

Les objectifs
Peuvent être par exemple :
- 90% des patients bénéficient d’un diagnostic dès leur sortie de l’établissement de santé
- 80% des patients passent moins de 5 heures dans l’établissement
=>On retrouve ici les notions d’amélioration du temps d’écoulement. Il s’agit de satisfaire les patients en raccourcissant le temps entre le début et la fin du processus, en apportant une réponse plus rapide. De tels résultats s’obtiennent notamment en travaillant sur les Mudas.
3.2- Exemple 2 : Traitement d’une demande de crédit dans un établissement bancaire
Lorsque des particuliers demandent un crédit à la consommation, ils doivent constituer un dossier, le présenter à leur établissement bancaire ou assimilé, puis ce dossier est analysé par un ou plusieurs intervenants en vue de faire une proposition de crédit adaptée au client, ou de lui transmettre une réponse négative, idéalement argumentée.
Dans ce cas-ci :
Processus analysé : Le traitement de la demande de crédit
Objet suivi dans le processus : Le dossier du client
Dans le processus optimisé : Le client obtient sa réponse dès son premier rendez-vous avec son conseiller et le taux de réponses positives est élevé.
Dans le processus non optimisé : Le client attend sa réponse plusieurs semaines, voire n’a pas de réponse du tout, et une grande partie des demandes ne reçoit pas de réponse positive.
Les objectifs
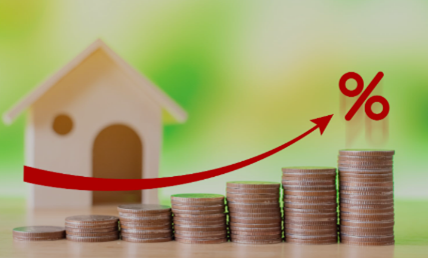
Ici les objectifs peuvent viser à ce que
- Le taux de validation des demandes passe de 20% à 50%.
- Le taux de validation des demandes à la première soumission passe de 5% à 40%.
- Le délai de réponse soit de moins de 7 jours dans 80% des cas.
è Il s’agit ici d’améliorer la qualité du service rendu et à nouveau de diminuer le temps d’écoulement. Un des axes de travail pourra concerner la mise en place et l’amélioration des standards.
3.3- Exemple3 : Étude de Cas Lean dans un Service de Support Client en Ligne
Contexte : Un service de support client en ligne souhaite améliorer la qualité des réponses aux clients tout en réduisant les temps d’attente.
Problème Initial : Les clients se plaignent de délais d’attente élevés et de réponses incorrectes ou incomplètes.
Implémentation Lean
1/ Analyse des Flux de Travail
– Identification des étapes du processus de gestion des tickets de support.
– Cartographie des flux pour comprendre la séquence des activités.
2/ Réduction des Temps d’Attente
- Introduction d’un système de tri des tickets basé sur la priorité et la complexité.
- Formation du personnel sur la gestion efficace des tickets prioritaires.
- Formation et Standardisation :
- Formation du personnel sur les procédures standardisées pour résoudre les types de problèmes courants.
- Création d’une base de connaissances accessible pour les agents et les clients.
3/ Utilisation de Poka-Yoke
- Intégration de vérifications automatisées pour détecter les réponses incorrectes.
- Utilisation de modèles de réponses standardisés pour minimiser les erreurs humaines.
4/ Feedback Client
- Mise en place d’enquêtes de satisfaction client après chaque interaction.
- Utilisation des commentaires clients pour ajuster les processus et les formations.
5/ Résultats

Les temps d’attente ont été réduits de 20%, et la qualité des réponses a augmenté de manière significative. La satisfaction client a considérablement augmenté, et le service de support est devenu plus efficace.
è Ces études de cas démontrent comment les principes Lean peuvent être appliqués avec succès dans des services non manufacturiers pour améliorer l’efficacité opérationnelle et la satisfaction client.
Chapitre 6 : Gestion des Ressources Humaines dans un Environnement Lean
1.Engagement des employés
Le Lean Management, au-delà d’être un ensemble de méthodes, repose sur le facteur humain. L’implication et l’engagement des employés sont des éléments cruciaux dans un environnement Lean. Un personnel engagé et impliqué est plus enclin à contribuer activement à l’amélioration continue, à adopter les changements et à participer à la réalisation des objectifs organisationnels. Voici quelques aspects à considérer pour promouvoir l’implication et l’engagement des employés dans un contexte Lean :
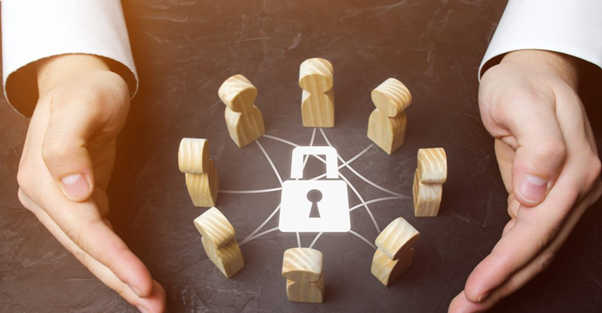
1.1- Communication Transparente
Communication Régulière : Maintenir une communication transparente, ouverte et régulière pour informer les employés des progrès, des résultats, et des changements planifiés.
Canal de Feedback : Créer des canaux de feedback pour permettre aux employés de partager leurs idées, leurs préoccupations et leurs suggestions d’amélioration.
1.2- Participation Active

Initiatives Kaizen : Encourager la participation active aux initiatives Kaizen (amélioration continue). Impliquer les employés dans l’identification des problèmes, la proposition de solutions, et la mise en œuvre des changements.
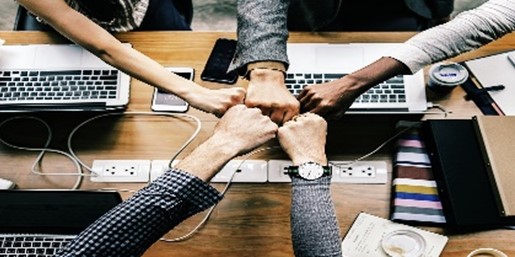
Groupes de Travail : Créer des groupes de travail interfonctionnels pour collaborer sur des projets spécifiques d’amélioration des processus.
1.3- Reconnaissance Publique
Valorisation et reconnaissance publique : les contributions positives des employés à l’amélioration continue. Cela peut être fait lors de réunions d’équipe, par le biais de newsletters internes, ou d’autres moyens de communication.
Récompenses : Mettre en place des systèmes de récompenses qui reconnaissent les efforts exceptionnels des employés dans la mise en œuvre des principes Lean.
1.4- Développement Professionnel
Opportunités de Formation : Offrir des opportunités de développement professionnel liées au Lean. Cela peut inclure des formations spécifiques, des certifications Lean, et des programmes de mentorat.
Utilisation des Compétences : Encourager les employés à utiliser et à développer leurs compétences dans le cadre de projets. Cela favorise un sentiment d’accomplissement et de progression.
1.5- Création d’un Environnement de Confiance

Écoute Active : Pratiquer l’écoute active pour comprendre les préoccupations des employés et démontrer que leurs opinions sont valorisées.
Transparence : Être transparent sur les décisions et les raisons qui motivent les changements, renforçant ainsi la confiance au sein de l’équipe.
1.6- Alignement avec les Objectifs Personnels
Clarté des Objectifs : S’assurer que les objectifs personnels des employés sont alignés sur les objectifs de l’entreprise.
Développement de Carrière : Montrez comment l’implication dans les initiatives Lean peut contribuer au développement professionnel des employés :
=> En favorisant l’implication et l’engagement des employés dans un environnement Lean, les organisations peuvent créer une culture de collaboration, d’amélioration continue, et de responsabilisation, ce qui contribue à des résultats durables et positifs.
2.Leadership Lean
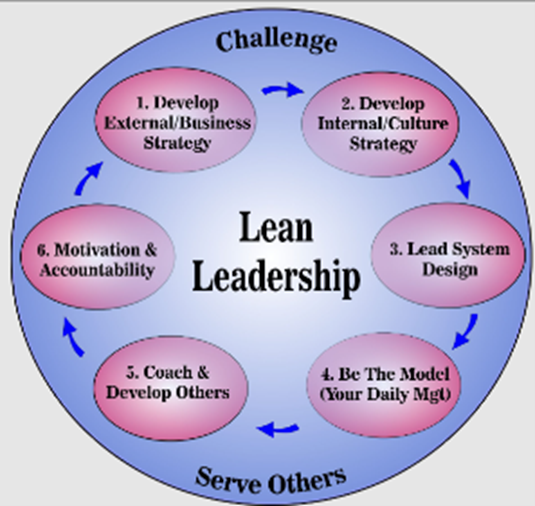
Le Leadership Lean a des implications significatives pour la gestion des ressources humaines (GRH). L’application des principes Lean dans la GRH vise à créer un environnement de travail efficace, flexible et axé sur la valeur ajoutée pour les employés et l’organisation dans son ensemble.
Voici quelques façons dont le Leadership Lean peut influencer la gestion des ressources humaines :
2.1- Respect des personnes
Le principe du respect des personnes dans le Leadership Lean se traduit par la reconnaissance de la valeur unique de chaque employé. Les pratiques de GRH doivent favoriser un environnement où les compétences, les idées et les contributions de chacun sont respectées et valorisées.
2.2- Responsabilisation et autonomie
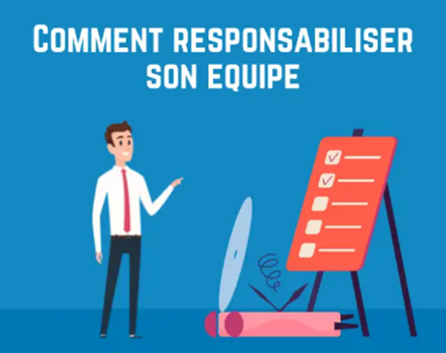
Le Leadership Lean encourage la responsabilisation des employés. Cela signifie donner aux individus les moyens de prendre des décisions autonomes, de résoudre les problèmes et de contribuer à l’amélioration continue. La GRH peut soutenir cela en favorisant un leadership décentralisé et en offrant des opportunités de développement professionnel.
2.3- Formation et développement continu
Pour favoriser l’amélioration continue, la GRH doit mettre en place des programmes de formation et de développement qui permettent aux employés d’acquérir de nouvelles compétences et de rester adaptatifs aux changements.
2.4– Flexibilité et agilité
Le Leadership Lean promeut la flexibilité. La GRH doit être capable de s’adapter rapidement aux changements, que ce soit dans les compétences requises, les structures d’équipe ou les processus de travail. Cela peut impliquer des stratégies de recrutement flexibles et des pratiques de gestion du personnel qui permettent une réponse rapide aux besoins changeants.
2.5– Communication transparente
La transparence est un élément clé du Lean. La GRH doit faciliter une communication ouverte et transparente entre la direction et les employés, favorisant ainsi la compréhension mutuelle des objectifs organisationnels et des attentes.
2.6- Amélioration continue des processus RH
Appliquer le principe d’amélioration continue à la GRH signifie constamment évaluer et améliorer les processus liés à la gestion des talents, du recrutement, de la formation, de l’évaluation de la performance, etc.
2.7- Gestion visuelle
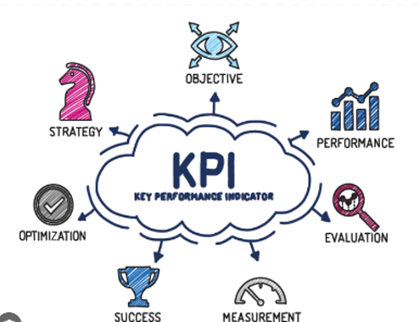
Utiliser des outils visuels, tels que des tableaux de bord ou des indicateurs de performance clés (KPI), peut aider à rendre les processus RH plus transparents et à permettre une gestion basée sur les données.
En résumé, le Leadership Lean dans la gestion des ressources humaines cherche à créer un environnement où les personnes sont respectées, responsabilisées, formées de manière continue et où les processus sont optimisés pour maximiser la valeur ajoutée. Cela contribue à construire une organisation plus agile, efficiente et centrée sur le
3.Culture organisationnelle Lean
Créer un environnement où les employés se sentent à l’aise de partager leurs idées d’amélioration. Mettre en place des mécanismes formels pour collecter les suggestions des employés.
3.1- Flexibilité et Polyvalence
Encourager la formation polyvalente pour permettre aux employés d’acquérir différentes compétences. Cela facilite la flexibilité dans l’affectation des tâches et la résolution de problèmes.
3.2- Mesure de la Performance
Mettre en place des indicateurs de Performance adaptés (KPI), partager régulièrement ces indicateurs pour évaluer les progrès.
3.3- Équilibre Travail-Vie Personnelle
- Charge de Travail Gérable : Veiller à ce que les employés ne soient pas surchargés de travail. Une charge de travail excessive peut entraîner la fatigue et réduire la productivité.
- Gestion du Stress : Offrir des ressources et des programmes pour aider les employés à gérer le stress, en particulier lors de périodes de changement important.
3.4- Récompenses et Reconnaissance
Mettre en place un système de récompenses qui reconnaît et valorise les efforts liés à l’amélioration continue. Cela peut inclure des récompenses financières, des reconnaissances publiques, ou des opportunités de développement professionnel.
3.5- Éthique et Respect
Respect des Individus : Assurer un environnement de travail respectueux où chaque employé se sent valorisé. Le Lean repose sur le respect des individus et de leurs contributions.
Chapitre 7 : Mise en Œuvre du Lean Management
1.Étapes de la mise en œuvre du Lean
La mise en œuvre du Lean, une approche de gestion axée sur l’élimination du gaspillage pour améliorer l’efficacité et la qualité, implique plusieurs étapes clés. Voici une description générale des étapes de mise en œuvre du Lean :
1.1- Formation et sensibilisation
Formation aux Principes Lean : S’assurer que les employés comprennent les principes Lean, les objectifs de l’entreprise en matière d’amélioration continue, leurs expliquer comment leur rôle contribue à la réalisation de ces objectifs.
Sensibilisation aux Enjeux : Expliquer les enjeux actuels de l’entreprise et les objectifs à atteindre.
1.2- Évaluation de l’état actuel (VSM)
Réaliser une évaluation approfondie des processus actuels de l’organisation en utilisant des outils tels que le Value Stream Mapping (cartographie des flux de valeur). Cela permet d’identifier les sources de gaspillage, les temps d’attente, les retards et autres inefficacités.
1.3- Établissement d’une vision Lean et des objectifs
Définir une vision claire de ce que le Lean devrait accomplir pour votre organisation. Établissez des objectifs spécifiques et mesurables qui correspondent à cette vision. Cela peut inclure des objectifs liés à la réduction des délais de production, à l’amélioration de la qualité, à la diminution des coûts, etc.
1.4- Formation continue et création de groupes Lean
Assurer-vous que les employés sont formés en continu sur les outils et les techniques Lean. Créez des équipes ou groupes Lean responsables de la mise en œuvre sur le terrain. Ces groupes peuvent être chargés de résoudre des problèmes spécifiques, d’implémenter des changements et de surveiller les progrès.
1.5- Mise en œuvre des principes Lean
Appliquer les principes Lean, tels que le 5S (tri, ranger, nettoyer, standardiser, maintenir), le juste-à-temps, et le kaizen (amélioration continue), dans les processus de l’organisation. Cela peut impliquer des ajustements dans la disposition des postes de travail, la réorganisation des flux de travail, et l’optimisation des stocks.
1.6- Visualisation et communication
Mettre en place des tableaux de bord visuels pour suivre les performances et les progrès vers les objectifs Lean. Assurez-vous que les informations importantes, telles que les indicateurs de performance clés (KPI), sont clairement visibles. La communication régulière sur les progrès et les succès est essentielle pour maintenir l’engagement de tous.
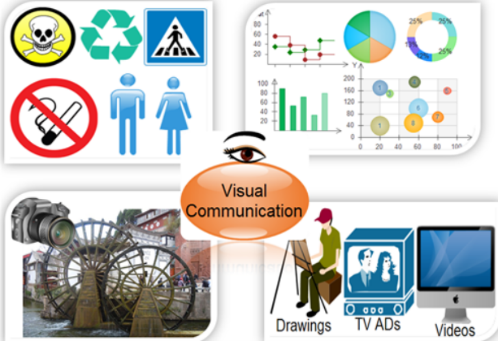
1.7- Mesure et évaluation continue
Mettre en place un système de mesure continue pour évaluer les améliorations et ajustez les processus en conséquence. Les indicateurs de performance doivent être régulièrement évalués pour garantir que les objectifs Lean sont atteints et pour identifier de nouvelles opportunités d’amélioration.
1.8- Élargissement de la portée et pérennisation

Une fois que des améliorations initiales ont été mises en œuvre avec succès, élargissez la portée du Lean à d’autres départements ou processus. Assurez-vous que les principes Lean sont intégrés dans la culture organisationnelle pour une pérennisation à long terme.
2.Surmonter les résistances au changement
La résistance au changement est un défi fréquent lors de la mise en œuvre de méthodologies Lean ou de tout autre processus de transformation organisationnelle. Surmonter ces résistances est essentiel pour assurer le succès du Lean. Voici quelques stratégies pour gérer la résistance au changement dans un contexte Lean.
2.1- Communication claire et ouverte
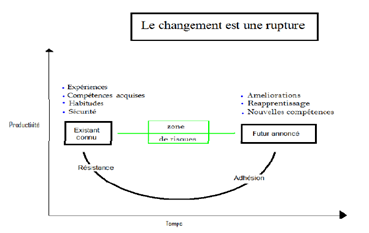
Communiquez de manière transparente et constante sur les raisons du changement, les avantages escomptés et les impacts potentiels sur l’organisation. Assurez-vous que les membres du personnel comprennent la nécessité du changement et soient informés à chaque étape du processus.
2.2- Formation adéquate
Fournissez une formation approfondie sur les concepts Lean et sur la manière dont ils s’appliquent à chaque individu dans l’organisation. Cela peut aider à dissiper les craintes liées à l’inconnu et à renforcer la confiance en fournissant aux employés les compétences nécessaires pour réussir dans le nouvel environnement.
2.3- Participation et implication
Impliquez les membres du personnel dans le processus de changement. Sollicitez leurs idées, préoccupations et suggestions. La participation active permet aux employés de se sentir davantage investis dans le processus de changement et peut atténuer les résistances.
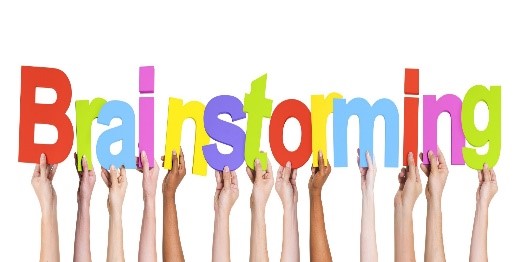
2.4- Leadership fort et exemplaire
Les leaders jouent un rôle crucial dans la gestion du changement. Montrez l’exemple en adoptant les principes Lean et en démontrant l’engagement envers la transformation. Les leaders qui incarnent la vision du changement et qui sont visibles dans leur soutien peuvent inspirer la confiance.
2.5- Gestion des craintes et des incertitudes

La résistance au changement est souvent alimentée par la peur de l’inconnu. Gérez les craintes en fournissant des informations précises sur les changements prévus, en anticipant les questions et en créant un espace pour les discussions ouvertes.
2.6- Reconnaissance et célébration des succès
Célébrez les petites victoires et reconnaître les contributions de chacun à la réussite du changement. Cela renforce une culture positive et encourage l’acceptation continue du Lean.
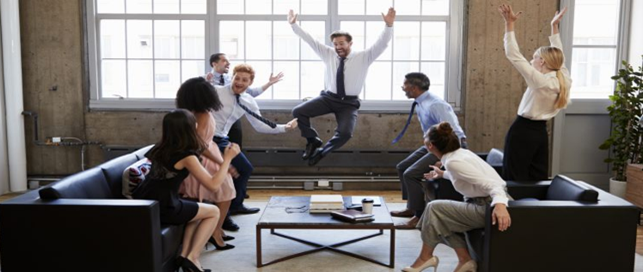
2.7- Adaptation progressive
Laissez de la place pour des changements progressifs. Si le changement est trop radical, cela peut provoquer une résistance accrue. Une transition progressive permet aux membres de l’organisation de s’adapter graduellement aux nouvelles façons de faire.
2.8- Gestion des conflits de manière constructive
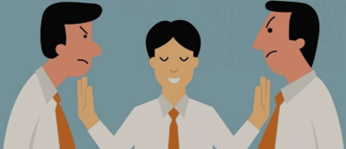
Envisagez des mécanismes pour résoudre les conflits de manière constructive. Écoutez les préoccupations et travaillez ensemble pour trouver des solutions qui répondent aux besoins de chacun.
2.9- Évaluation continue et ajustements
Soyez prêt à ajuster la mise en œuvre du Lean en fonction des retours d’expérience et des résultats obtenus. L’adaptabilité est essentielle pour répondre aux préoccupations légitimes et apporter des améliorations continues.
En adoptant ces stratégies, les organisations peuvent atténuer la résistance au changement et faciliter une transition plus fluide vers une culture Lean. La compréhension, la communication efficace et la participation active sont des clés importantes pour surmonter les résistances au changement.
3.Évaluation des résultats et ajustements
L’évaluation des résultats et les ajustements sont des étapes cruciales dans le processus Lean, car elles permettent de mesurer l’impact des changements apportés et d’apporter des améliorations continues. Voici quelques étapes importantes pour évaluer les résultats et effectuer des ajustements dans un environnement Lean :
3.1- Définir les indicateurs de performance clés (KPI)

Avant même de commencer la mise en œuvre du Lean, identifiez et définissez des indicateurs de performance clés qui reflètent les objectifs de votre organisation. Ces KPI peuvent inclure des mesures telles que le temps de cycle, la qualité, la productivité, les coûts, etc.
3.2- Mesurer les résultats initiaux
Effectuez des mesures initiales pour établir une base de référence avant la mise en œuvre des changements Lean. Cela vous permettra de comparer les performances avant et après les modifications.
3.3- Évaluer les impacts sur la chaîne de valeur
Analysez les impacts des changements sur l’ensemble de la chaîne de valeur de l’organisation. Cela peut inclure la réduction des temps d’attente, l’amélioration de la fluidité des processus, et l’optimisation des ressources.
3.4- Solliciter des retours d’expérience
Demandez des retours d’expérience auprès des membres de l’équipe impliqués dans la mise en œuvre du Lean. Leurs observations et commentaires peuvent fournir des informations précieuses sur les aspects positifs et les éventuels points d’amélioration.
3.5- Analyser les écarts par rapport aux objectifs
Comparez les résultats obtenus avec les objectifs définis au départ. Identifiez les écarts et analysez les raisons derrière ces différences. Cela peut révéler des opportunités d’ajustements.
3.6- Encourager l’amélioration continue
Promouvez une culture d’amélioration continue en encourageant les membres de l’organisation à identifier des opportunités d’amélioration et à proposer des idées. L’engagement de tous les niveaux de l’organisation est essentiel.
3.7- Ajuster les processus et les pratiques
Sur la base des résultats et des retours d’expérience, effectuez des ajustements aux processus et aux pratiques Lean. Cela peut impliquer des modifications dans la conception des postes de travail, la réorganisation des flux de travail, ou l’optimisation des procédures.
3.8- Réaliser des cycles PDCA
Utilisez le cycle PDCA (Plan-Do-Check-Act), également connu sous le nom de cycle d’amélioration continue, pour planifier, mettre en œuvre, vérifier les résultats et ajuster en conséquence. Ce processus cyclique favorise une approche itérative de l’amélioration continue.
3.9- Communiquer les résultats et les ajustements
Communiquez de manière transparente les résultats obtenus, les ajustements apportés et les leçons apprises à toute l’organisation. La communication ouverte contribue à maintenir l’engagement et à favoriser une compréhension partagée des bénéfices de la démarche Lean.
3.10- Réitérer le processus
La démarche Lean est un processus continu. Après avoir ajusté les pratiques et réalisé des améliorations, réitérez le cycle en mesurant à nouveau les résultats et en continuant à chercher des opportunités d’amélioration.
L’évaluation continue et les ajustements réguliers sont essentiels pour garantir que la mise en œuvre du Lean reste alignée sur les objectifs organisationnels et réponde aux évolutions du marché et des besoins des clients. En adoptant une approche itérative et réactive, une organisation peut maintenir un état d’amélioration continue dans un environnement Lean.